Commitment to quality
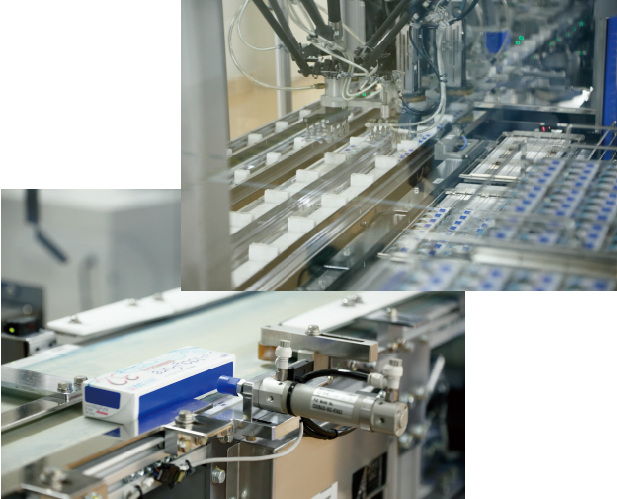
Our domestically manufactured, daily disposable contact lenses such as SEED 1dayPure moisture, SEED 1dayPure moisture for Astigmatism and SEED 1dayPure Multistage are the fruits of our technology, representing the commitment of SEED to the quality of its domestic manufacturing. In these products, SEED has leveraged its accumulated strength in technology, research and development and has done everything by itself, from the development of materials to the establishment of production technology. Each of these product items is the only one of its kind, is superior to all other manufacturers’ products in terms of power within the range of manufacturing and is capable of precisely satisfying customers’ needs (according to research conducted by SEED).
In 2007, the SEED Konosu Research Institute was established to serve as our hub for the research, development and manufacture of our disposable contact lenses. This led to the launch of SEED 1dayPure, the first daily disposable contact lens manufactured in Japan, in 2009. Today, it has been upgraded to SEED 1dayPure moisture, and its sales have increased nearly fourfold in comparison with the first year of its launch. The domestic share of the product is increasing.
In August 2014, the construction of Building 2 was completed for use as a new hub for our production activities. In June 2016, a new research building was constructed for the purpose of facilitating applied research in new materials, new functional lenses and others. In September 2017, the construction of Building 3 was completed for the purpose of facilitating continued improvements of our manufacturing capacity and the manufacture of new products. This enables us to achieve greater consistency in the supply of our products while also adapting to the practice of manufacturing multiple product items in small quantities.
About Konosu Research Institute
- [Technological strength]
- SEED manufactures many of its devices and materials domestically, including dies, moldings (resin) and devices for the manufacture of contact lenses, inspection devices, the materials necessary for the devices, and many others. The manufacture of “Made in Nippon” high-quality contact lenses has continued since 1957.
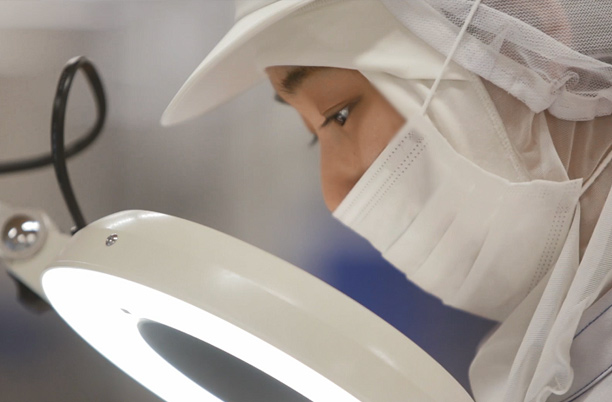
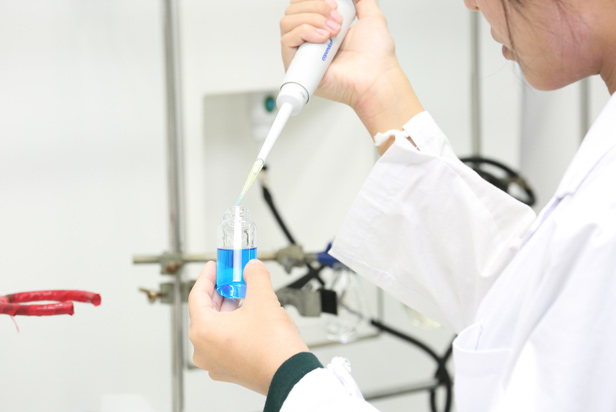
- Visual inspection performed of all products
- The process for the manufacture of disposable contact lenses can be largely divided into three steps: drying (forming a lens), moistening (filling a container with preservation solution and packing the lens) and packing (the container into an outer case). In all of these steps, we perform image inspections to visually check all products. In the past, visual inspections were performed by human eyes. Some of our colleagues who had received training at a manufacturing site introduced automatic inspection devices to all of our processes. As a consequence, this has enabled us to save time and costs in performing inspections while keeping the quality of the domestically manufactured products as high as before.
- Open innovation
- The research and development of the Pure Series, the staple products of SEED, have been undertaken entirely on an in-house basis. The 100% domestically manufactured contact lenses, the first of their kind in Japan, are recognized for their “Made in Nippon” quality and are highly regarded overseas as well as in Japan. To expand our share, however, we must satisfy diversifying needs promptly.
To this end, SEED implements open innovation, involving proactive collaboration with many different enterprises, universities and research institutes, as well as our in-house research. Through collaborative research with different business categories and industries, we pursue the development of groundbreaking, next-generation contact lenses.
Balancing the in-house research (inward) and open innovation (outward) cultivates flexible thinking, a very important skill of researchers. SEED is also committed to systematically allowing young researchers to collaborate aggressively with the outside.
- [Process for manufacturing]
- ur lens design division is working closely with our clinical division, and provides a diverse range of designs for contact lenses to make them comfortable for the eyes. The exchange of information with staff members with extensive clinical experience is rapidly reflected in the design of our lenses. Today, we offer 6,275 products with different specifications (*as of December 1, 2017).
【Lathe-cut method】 Cut rod-like material into a button, shave and polish the inner and outer surfaces and finish it into a lens form.
【Cast-mold method】 Cast the raw material of the contact lens into a front curve mold. Then layer a base curve mold onto it to make the lens.